Custom SLS 3D Printing: Tailored Solutions for Precision Manufacturing

Custom Selective Laser Sintering (SLS) 3D printing is revolutionizing the way industries design and manufacture complex, high-performance parts. Unlike traditional manufacturing methods, SLS uses a laser to fuse powdered materials layer by layer, enabling unparalleled design flexibility, durability, and precision.
From aerospace components to medical implants, custom SLS 3D printing allows businesses to create bespoke parts tailored to exact specifications without costly tooling. This article explores the advantages, materials, applications, and future trends of custom SLS 3D printing, demonstrating why it’s a game-changer for modern manufacturing.
How Custom SLS 3D Printing Works
The Custom SLS 3D printing process involves several critical stages:
-
Digital Design Preparation – A 3D model is created using CAD software and optimized for printing.
-
Powder Layering – A fine layer of thermoplastic or metal powder is spread across the build platform.
-
Laser Sintering – A high-powered laser selectively fuses the powder particles based on the digital design.
-
Cooling & Post-Processing – The printed part cools, and excess powder is removed. Additional finishing (sanding, dyeing, or coating) may be applied for enhanced aesthetics and functionality.
Since SLS doesn’t require support structures, it allows for intricate geometries, hollow sections, and interlocking parts that would be impossible with traditional methods.
Key Benefits of Custom SLS 3D Printing
1. Unmatched Design Freedom
Custom SLS printing enables the production of complex, lightweight structures such as lattices, internal channels, and organic shapes. This is ideal for industries like aerospace and automotive, where weight reduction and strength are critical.
2. High-Performance Materials
SLS supports a wide range of engineering-grade materials, including:
-
Nylon (PA12, PA11) – Strong, flexible, and chemical-resistant, perfect for functional prototypes.
-
Glass-Filled Nylon (PA-GF) – Adds stiffness and heat resistance for industrial applications.
-
TPU (Thermoplastic Polyurethane) – Used for elastic, rubber-like components.
-
Metal Powders (Aluminum, Titanium, Stainless Steel) – Ideal for high-strength, heat-resistant parts.
3. Cost-Effective for Custom & Low-Volume Production
Unlike injection molding, which requires expensive molds, SLS allows for cost-effective small-batch production. Businesses can manufacture custom parts on demand without upfront tooling costs.
4. Faster Time-to-Market
With rapid prototyping capabilities, custom SLS printing accelerates product development cycles, reducing lead times from weeks to days.
Industries Leveraging Custom SLS 3D Printing
1. Aerospace & Defense
Aerospace manufacturers use SLS to produce lightweight, high-strength components like ducting, brackets, and drone parts. The ability to optimize designs for weight and performance is crucial for fuel efficiency and durability.
2. Medical & Dental
Custom SLS printing enables patient-specific solutions such as:
-
Surgical guides – For precise implant placement.
-
Prosthetics & Orthotics – Tailored for comfort and functionality.
-
Dental Aligners & Crowns – Made from biocompatible materials.
3. Automotive & Motorsports
From custom intake manifolds to lightweight dashboard components, SLS helps automotive engineers create durable, high-performance parts quickly.
4. Consumer Products & Wearables
Companies use SLS to manufacture ergonomic designs for:
-
Custom-fit eyewear & helmets
-
Durable phone cases & electronic housings
-
Fashion accessories with intricate patterns
The Future of Custom SLS 3D Printing
As additive manufacturing evolves, several trends are shaping the future of custom SLS printing:
-
Multi-Material Printing – Combining different powders in a single print for hybrid-material components.
-
AI-Driven Optimization – Machine learning improves print accuracy and reduces material waste.
-
Sustainable Manufacturing – Recycling unused powder and using bio-based materials to reduce environmental impact.
-
Large-Scale Industrial SLS – Newer machines with bigger build volumes enable the production of larger functional parts.
Conclusion
Custom SLS 3D printing is transforming industries by offering unparalleled design flexibility, material versatility, and cost-effective production. Whether for prototyping, end-use parts, or highly specialized components, SLS provides a competitive edge in today’s fast-paced manufacturing landscape.
What's Your Reaction?
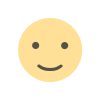
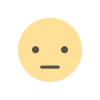
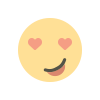

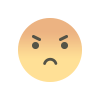
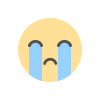
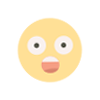